PET bottle & juice cup manufacturing in chennai
PET bottle manufacturing and juice cup manufacturing both involve the production of containers specifically designed for holding beverages. Here’s an overview of each manufacturing process:
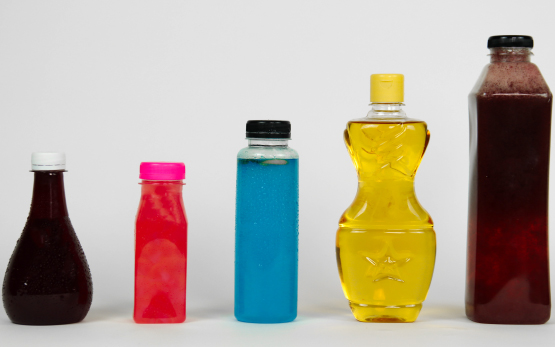
PET Bottle Manufacturing
PET Resin Preparation
PET resin, along with additives and stabilizers, is prepared and processed to achieve the desired properties in the final bottle. The resin is usually in the form of pellets.
Bottle Production
The PET resin is melted and injected into a preform mold using injection molding machines. The preforms are then cooled and solidified to form the desired shape, which is a partially formed bottle with a threaded neck.
Stretch Blow Molding
The preforms are transferred to stretch blow molding machines, where they undergo a two-stage process. In the first stage, the preforms are reheated and stretched in length. In the second stage, the preforms are blown into the final bottle shape using compressed air.
Quality Control
Throughout the manufacturing process, strict quality control measures are implemented to ensure that the PET bottles meet the required specifications. This includes inspecting the bottles for defects, checking their weight and dimensions, and conducting tests to ensure their strength and integrity.
Finishing and Packaging
After quality control checks, the PET bottles go through finishing processes such as trimming excess materials, smoothing edges, and applying labels or printing. The finished bottles are then packaged and prepared for distribution.

Juice Cup Manufacturing in chennai
Material Selection
Food-grade materials such as plastic (including PET), paper, or foam are selected based on the desired properties of the cups.
Cup Forming
The chosen material is processed through cup forming machines, which use techniques like thermoforming or injection molding to shape the material into cup forms. Thermoforming involves heating the material and then shaping it using a mold, while injection molding injects molten material into a mold to form the cups.
Printing and Customization
Cups can be customized with branding elements, logos, designs, or labeling based on customer requirements. Printing processes such as flexographic printing or digital printing may be used for customization.
Quality Control
Quality control measures are implemented to ensure that the cups meet the required standards. This involves inspecting the cups for defects, checking their size and dimensions, and conducting tests for strength and functionality.
Finishing and Packaging
Once the cups pass quality control checks, any necessary finishing touches such as trimming excess materials or smoothing edges may be performed. The cups are then carefully packaged to protect them during transportation and storage.